記事公開日
最終更新日
在庫管理とは?目的や方法、メリットなどを解説
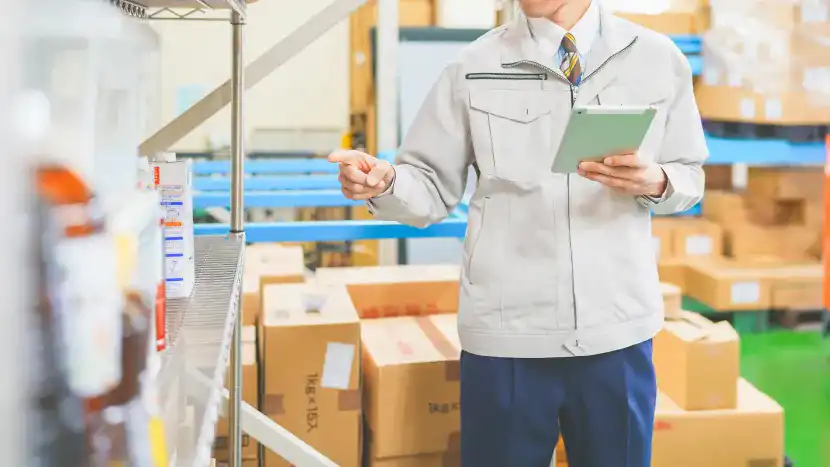
製造業において在庫管理は、生産スケジュールに沿って適切な原材料・部品などを供給するために必要な業務です。
在庫管理の精度は、企業の生産性やコストに大きな影響を与えます。
そんな重要な在庫管理ですが、在庫の種類が増えるほどに業務が複雑化しやすく、効率的な管理が難しいと感じている人も多いのではないでしょうか。
そこで本記事では、そもそも在庫管理とはどんな業務なのか、目的や具体的な流れについて解説します。
在庫管理の効率化に役立つシステムも紹介するので、ぜひ最後までチェックしてみてください。
これを読めば、在庫管理を行う本来の目的や正しい流れが理解でき、在庫管理の効率化による生産効率アップやコストカットを狙うためのヒントが得られるでしょう。
在庫管理とは
在庫管理とは、保管している製品や部品の数量・場所・品質を適切な状態に維持・管理する業務のことです。
生産計画に応じた適切な部品供給が求められる製造業においては、特に在庫管理業務の精度が生産性やコストに大きく影響します。
在庫管理業務で管理するものは、主に以下の4つです。
- 原材料:製品を作るための素材など
- 部品:組み立てに使うパーツなど
- 仕掛品:製造途中のもの
- 製品:完成した商品
在庫管理の業務では、在庫が多すぎず少なすぎない適量を維持する必要があります。
過剰在庫は保管場所のスペースが不足したり、倉庫のコストが上がったりする原因です。
反対に在庫が少なすぎると、生産計画に支障が出る可能性があります。
在庫管理の目的
在庫管理業務の主な目的としては、以下の3つが挙げられます。
- 生産性の向上
- コストの削減
- キャッシュフローの安定化
それぞれの目的について、詳しくチェックしておきましょう。
生産性の向上
在庫管理の目的の1つは、生産性の向上です。
在庫管理では、部材や製品の数量・場所・品質を適切な状態に維持・管理することで、生産性の向上に寄与します。
正しい在庫管理が行われていない状態と比べると、その効果は明確です。
<在庫管理による生産性向上の例>
在庫管理が適切 | 在庫管理が不適切 | |
---|---|---|
数量 |
|
|
場所 |
|
|
品質 |
|
|
在庫管理で、原材料・部品の在庫数を適量に保てば、生産計画に応じて必要な原材料・部品を供給できます。
製品在庫についても同様で、注文が入ったらすぐに製品を出荷できるため、機会損失のリスクを低減可能です。
在庫の場所を把握することも大切です。
たとえ必要な在庫数があったとしても、保管場所がわからなければ生産や販売の計画に悪影響を及ぼす可能性があります。
また、在庫の場所が把握できていない場合、棚卸などに時間がかかりミスしやすくなる点もリスクです。
在庫管理で原材料・部品・製品などの品質を管理することで、不良品の流通リスクを低減できます。
仮に不良品が発生した場合にもロットなどが管理できていれば、影響を最小限に抑えることが可能です。
コストの削減
在庫管理によるコスト削減は、主に在庫の抱えすぎによる管理コストの節約です。
生産計画に必要な在庫を供給するためには十分な在庫量の確保が必要ではあるものの、在庫が多すぎると管理にかかる費用が大きくなります。
在庫管理にかかる費用は、主に以下の3つです。
<在庫管理にかかる費用>
費用 | 例 |
---|---|
保管費 | 倉庫レンタル費用・空調費用 |
管理費 | 人件費・設備費(フォークリフトなど) |
廃棄費 | 使用期限切れの在庫の廃棄にかかる費用など |
在庫の数量が増えるほど保管スペースが必要となるため、倉庫や棚の使用にかかる費用が増加します。
また、温度管理が必要な部材の場合、保管スペースの広さに応じた空調費用がかかる点にも注意が必要です。
日常的な維持管理や棚卸を担当する人の人件費も、在庫数が多いほど高くなります。
フォークリフトなど、在庫を移動・保管するのに必要な設備費も同様です。使用期限が決まっている原材料は過剰在庫による廃棄リスクも見逃せません。
適切な在庫管理により在庫を正しく管理できれば、上記のような無駄なコスト増加を防止できます。
また、在庫管理システムを導入することで、現在発生している保管費・管理費・廃棄費の削減も期待できるでしょう。
キャッシュフローの安定化
キャッシュフローの安定化も、在庫管理の大切な目的の1つです。
キャッシュフローは資金(現金)の流れを示す言葉で、安定した経営のためには安定したキャッシュフローが必要不可欠だといえます。
在庫は会社の試算ではあるものの、倉庫に保管しているだけでは利益を生みません。
過剰在庫は会社の試算が倉庫で停滞している状態であり、長く続けばキャッシュフローの悪化を招きます。最悪の場合、資産はあるのに倒産する「黒字倒産」につながります。
適正在庫を意識して在庫の入出の流れをスムーズにすれば、キャッシュフローが安定化し、お金がうまく回るようになるでしょう。
在庫管理の流れ
在庫管理を始める際の流れを解説します。
一般的な在庫管理の流れは、以下のとおりです。
- 現在の在庫数と状態を把握する
- 適正な在庫量を定める
- 発注方法を決める
- 管理方法を定める
- PDCAを回して在庫管理を最適化する
それぞれのステップについて詳細を確認しておきましょう。
現在の在庫数と状態を把握する
まずは、現在自社で保管している在庫の種類・数量・場所・品質を把握します。
「どれだけの量が、どこに、どんな状態で保管されているか」を、原材料・部品・製品などの種類別に正確にチェックしましょう。
すでに帳簿やExcelなどで管理している場合は、記録されている在庫状況と実際の在庫状況に差がないか確認します。
数量や場所はもちろん、劣化・破損・使用期限切れなどの状態のチェックも大切です。
現在の在庫の状態を把握できたら、加工しやすいデータとしてまとめましょう。
次の適正な在庫量の設定には、在庫データの分析が必要不可欠です。
紙の帳簿よりも、Excelなどにまとめておくと加工・分析しやすいでしょう。
在庫状況の分析には、ABC分析や在庫回転率分析などがよく用いられます。
- ABC分析:売上や使用頻度などから在庫に優先順位を付ける分析手法
- 在庫回転率分析:一定期間内に在庫が入れ替わる回数を求める分析手法
分析結果は、適正在庫の見極めに役立てましょう。
適正な在庫量を定める
次に、過不足のない在庫数を意味する「適正在庫」を、原材料・部品・製品の種類ごとに設定します。
適正在庫の設定には、在庫量の変動や回転率の把握が必要です。
生産に関わる原材料や部品は生産管理部門、販売に関わる製品は販売管理部門など、別の部門とも必要に応じて連携しながら進めましょう。
原材料と部品には、発注から到着までにかかる時間(リードタイム)や、一度の発注で納品される数量(発注ロット)も影響するため、購買部門とのやり取りも必要です。
適正在庫は一般的に「サイクル在庫+安全在庫」で計算されます。
サイクル在庫は平常時の生産・販売によって流通する在庫のことで、安全在庫は緊急時用に念のため抱えておく在庫のことです。
在庫の種類別に、精度の高い適正在庫を設定しましょう。
発注方法を決める
適正在庫が決まったら、発注方法や管理方法を決定する必要があります。
一般的な発注方法は、定量発注と定期発注の2種類です。
定量発注方式では、在庫が一定数を下回った際に決まった数量を発注します。
一方、定期発注方式は、決まったタイミングで必要な数量を発注する方法です。
<定量発注と定期発注の決め方の目安>
発注方式 | 向いているケース | 向かないケース |
---|---|---|
定量発注 |
|
|
定期発注 |
|
|
定量発注方式は在庫数に応じて発注するため、需要が不安定な原材料・部品の発注に適しています。
在庫が一定数を下回ると発注されるため、欠品リスクも低めです。
定期発注と比べると最低限の在庫しか抱えないため、管理コストがかかる高価な部材・大きな部材にも向いています。
一方、部材によっては発注回数が多くなるため、発注自体にコストがかかるケースには不向きです。
また、各在庫の量を常に把握しておく必要があるうえ、発注が不定期になるため、やや発注業務が複雑化する点には注意しましょう。
定期発注方式は設定したタイミングで発注するため、需要が安定している部材の発注に適しています。
発注頻度が一定なので業務の簡素化も可能です。
部材によっては、一度にまとめて発注することによるコストメリットもあるでしょう。
一方、需要が変動しやすい部材の場合、定期発注では欠品・過剰在庫のリスクがあります。
在庫量によらず発注するため、保管スペースが狭い場合は場所が足りなくなる可能性がある点にも要注意です。
管理方法を定める
保管する在庫の管理方法を決めます。
紙の帳簿・Excel・在庫管理システムなどから、自社の在庫管理業務に適した管理方法を選択しましょう。
在庫の場所を把握するためのロケーション管理も重要です。
保管している場所や棚などと在庫を紐付けて管理し、必要なものをすぐに取り出せるようにします。
保管場所と在庫の紐付けには、バーコードやICチップを活用したシステムも便利です。
在庫管理の担当者や業務マニュアルなども決定する必要があります。
実際に在庫管理業務が行える体制を構築し、運用しながら課題や改善点を抽出しましょう。
PDCAを回して在庫管理を最適化する
在庫管理の方法は一度決めてしまえば終わりというわけではありません。
運用していくなかで課題や問題があれば、PDCAを回しながら改善していきましょう。
特に発注頻度は生産計画などの影響を大きく受けるため、欠品リスクが高まった際などは、早急な改善が必要です。
なお、PDCAとは、Plan(計画)・Do(実行)・Check(評価)・Action(改善)の頭文字を取ったフレームワークの名前です。
一度決めた在庫管理方法も定期的に効率や精度を評価し、必要に応じて改善することを意味しています。
在庫管理の方法とメリット
在庫管理の方法には、主に紙ベースの帳簿・Excel・在庫管理システムの3つがあります。
それぞれメリット・デメリットがあるため、自社の状況に合う方法を採用することが大切です。
<各在庫管理の方法のメリット・デメリット>
方法 | メリット | デメリット |
---|---|---|
紙ベース |
|
|
Excel |
|
|
在庫管理システム |
|
|
紙ベース
帳簿など紙ベースでの管理は、運用コストがほぼかからないのがメリットです。
管理する在庫の種類や数が少ないのであれば、ノート1冊で在庫管理ができる紙ベースの管理方法でも対応できるでしょう。
一方、在庫の種類や数が多くなると記入する情報量も増え、手書きでの管理が難しくなります。
作業が複雑化するとミスも起きやすくなるため、担当者が業務負荷を感じ始めたら、別の方法へ切り替えた方がよいでしょう。
Excel
表計算ソフトのExcelも、よく在庫管理に使われています。
手書きとは違って計算やグラフ化などを自動化できるのがメリットです。
Excelは他の業務にもよく使われるため、運用コストや担当者の学習コストは比較的低いといえるでしょう。
ただし、Excelは在庫管理専用のソフトではないため、使いやすくするための工夫は必要です。
カスタマイズをしすぎると業務が属人化したり、ミスが発生しやすくなったりするため注意しましょう。
在庫管理システム
在庫管理業務を効率化したい場合は、在庫管理専用のシステムの導入をおすすめします。
Excelとは違い、棚卸機能や在庫分析機能など最初から在庫管理に便利な機能を搭載しているのが特徴です。
在庫管理システムは、紙ベースやExcelでの管理と比べると導入・運用にコストがかかり、担当者のトレーニングも求められます。
とはいえ、導入によって在庫管理が最適化でき、管理にかかる人件費なども削減が期待できるため、導入メリットは大きいといえるでしょう。
まとめ
本記事では、在庫管理とは何か、目的や導入の流れについて解説しました。
在庫管理は適切に部材・商品を供給するために必要な業務で、企業の生産性向上・コスト削減・キャッシュフロー改善に寄与します。
在庫管理を始めるには、まず自社が保管する原材料・部品・製品などの在庫状況を確認し、適正在庫の設定が必要です。
発注方法や管理方法を定めたら、実際に運用しながらPDCAを回し、在庫管理業務の最適化を目指しましょう。
製品紹介
在庫管理業務の効率化には、種類別の在庫状況の見える化が必要不可欠です。
在庫状況を見える化して関係者に共有するステップでは、PIM(商品情報管理)システムが応用できます。
在庫管理システムと連携させて業務の効率化を目指すなら、商品情報管理システム「KOKONIDAS(ココニダス)」がおすすめです。
在庫管理を行っているExcelや各種在庫管理システムとKOKONIDASを連携すれば、各部品の在庫数・保管場所・入出庫履歴・仕入れ先・調達リードタイムといった在庫情報を管理できます。
情報はリアルタイムに更新され、権限のある社内関係者がチェック可能です。
KOKONIDASでは、拠点をまたぐ在庫情報の一元管理もできます。
拠点間での在庫配置の適正化を図りたいシーンでも活用しやすいでしょう。
また、管理しているデータは抽出して発注計画の分析にも活用できます。
<KOKONIDASの特徴>
特徴 | 概要 |
---|---|
汎用的なデータ構造で、項目の追加・編集が可能 | 取引先からの商品情報データ提供依頼に対して、加工などの手間なく必要な情報を共有できる |
提供先のフォーマットに適したデータのアウトプット | 複数の販売チャネルやプラットフォームへのデータ出力時、個別にデータを作成する手間は不要 |
システム開発不要なパッケージシステム | 導入が容易で費用も抑えられる |
充実のデータ制作支援 | 既存システムから情報を吸い上げてデータを制作・メンテナンスする作業のサポートを対応 |
KOKONIDASの詳しい機能や特徴はこちら
KOKONDASはデモ環境での無料体験もご利用いただけます。
在庫管理システムとPIMを連携した在庫管理の効率化を検討中の担当者様は、ぜひお気軽にお問い合せください。
KOKONIDASに関するお問い合わせはこちら