記事公開日
最終更新日
製造業におけるIoT化のメリットや活用例を解説
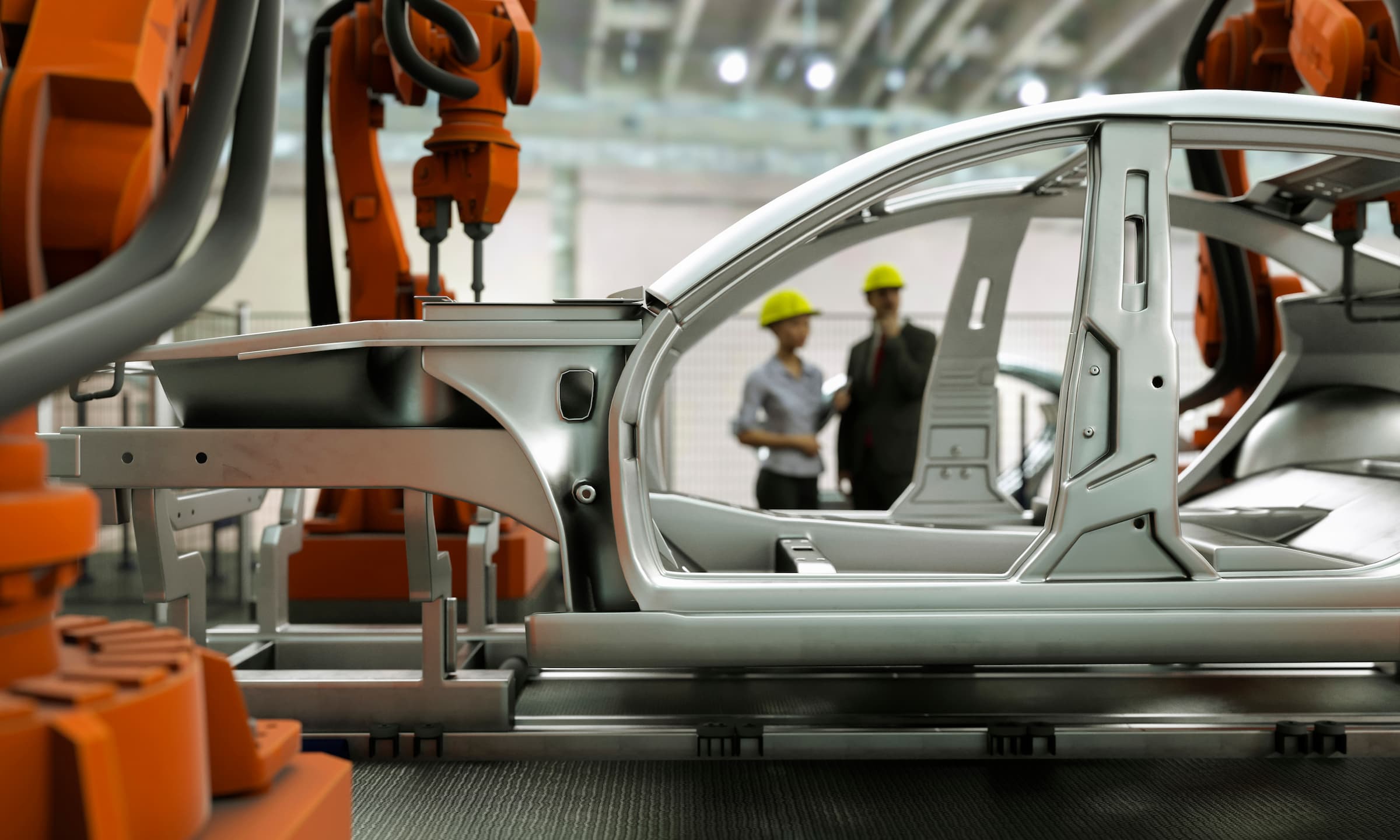
製造業におけるIoT化には、生産効率や品質を向上させるなどのメリットがあります。生産現場へのIoT技術の導入は、スマートファクトリーの実現にも必要不可欠です。
一方、現場のIoT化には綿密な計画が必要で、規模に応じたコストも発生することから、「製造業におけるIoT化のメリットを知ってから検討したい」「IoT技術の活用事例を知りたい」といった担当者様も多いのではないでしょうか。
そこで本記事では、製造業におけるIoT化によって実現できることや導入メリット、活用例などについて解説します。自社の生産現場にIoTの導入を検討中の方は、ぜひ参考にしてください。
IoTとは
IoT(Internet of Things)とは、「モノのインターネット」と訳される概念で、さまざまな「モノ」がインターネットを介して相互に接続され、情報のやり取りを行う技術のことです。
製造業においては、センサーを取り付けた機械や設備がインターネットを通じてデータを収集・送信し、それを基にした分析・制御が行われます。IoTを活用すれば、工場内の状況をリアルタイムで把握したり、効率的な生産計画を立てたりすることが可能です。
製造業においてIoT化でできること
製造業においてIoT化でできることとしては、以下の2つが挙げられます。
スマートファクトリーの実現
製造業におけるIoT化の代表的な成果の一つが、スマートファクトリーの実現です。スマートファクトリーとは、工場内の設備や装置・人・モノの動きなどをすべてデータ化し、それをもとに最適な生産活動を自律的に行う次世代型の工場を指します。
従来の工場では、現場での判断や経験則に頼っていた部分が多く、状況の把握や改善には時間がかかっていました。
IoTを導入すれば、各設備に取り付けたセンサーから稼働状況や温度・振動といったデータをリアルタイムで収集できます。そのデータをAIやビッグデータ解析と組み合わせて活用すれば、生産ラインのボトルネックを特定し、生産計画の最適化や故障予知も可能です。
さらに、クラウドを活用すれば遠隔地からでも生産状況の確認や操作ができるため、多拠点にまたがる工場を統合的に管理することも容易になります。これにより、品質向上、生産性の最大化、人件費削減といった複数のメリットを同時に実現することが可能です。
製品のIoT化
もうひとつが製品そのもののIoT化です。製造した製品にセンサーや通信機能を搭載し、ユーザーの使用状況や稼働状態をメーカー側で把握できるようにする取り組みです。
例えば、産業機械や大型設備にIoT機能を持たせれば、稼働時間・負荷状況・使用環境といったデータをクラウド経由で収集可能です。これにより、メーカーは顧客の実際の使用状況に基づいたメンテナンス提案や、故障リスクのある部品の早期交換を促すなど、より的確なアフターサービスが提供できます。
また、利用データを製品開発に活かすことも可能です。実際の利用現場から得たデータを分析すれば、製品の設計改善や新たな機能追加、カスタマイズ提案といった開発サイクルの高速化にもつながるでしょう。
製造業におけるIoT化のメリット
製造業におけるIoT化にはさまざまなメリットがあります。代表的なメリットは、以下の6つです。
データの可視化
IoT化によって得られる最も基礎的なメリットの一つがデータの可視化です。センサーを通じて収集された稼働状況・温度・湿度・振動・エネルギー消費量などのデータをリアルタイムで可視化することで、これまで人の目や経験に頼っていた現場判断が、客観的なデータに基づいたものに変わります。
例えば、生産ラインの遅延がどこで発生しているのか、どの設備に負荷がかかっているのか、無駄な待機時間はどこにあるのかといったことが明確になり、迅速な対応と改善が可能になります。見える化されたデータは、その後の分析や自動化の土台にもなるため、IoT化の第一歩としても重要です。
生産性の向上
IoTの活用により、生産工程のボトルネックの特定や、設備稼働率のリアルタイムでの監視が可能になります。その結果、稼働率の低い時間帯や非効率な工程を可視化でき、無駄な動作や停止時間を最小限に抑えることが可能です。
また、異常やトラブルが発生した場合にも、即座に通知が行われる仕組みを導入することで、迅速な対応が可能となり、全体としての稼働効率を向上させられます。さらには、設備の自動制御や予知保全といったIoT機能と組み合わせれば、生産工程がよりスムーズに稼働し、作業員の業務負担軽減にも貢献します。
結果として、生産量の向上と納期短縮の両立が実現し、生産性が向上します。企業全体の競争力強化も期待できるでしょう。
品質の向上
製造現場において、品質の安定性は企業の信用や顧客満足に直結する重要な要素です。
IoTを導入すれば、製造中の温度・圧力・湿度・部品の精度など、製品品質に関わるパラメータを常時監視できるようになります。リアルタイムでの異常検知により、製品に不具合が生じる前に対処できるようになり、結果的に不良品の発生率を大幅に削減することが可能です。
また、全ての生産データを記録・保存することで、トレーサビリティが強化され、万が一クレームや品質問題が発生した際にも、迅速かつ正確に原因を特定・対応できます。こうした品質の安定化は、ブランド価値の向上や顧客の信頼獲得にも大きく貢献するでしょう。
コスト削減
IoTの導入は初期費用がかかるものの、中長期的には大きなコスト削減効果をもたらします。
例えば、予知保全を活用すれば、突発的な機械故障によるライン停止を未然に防げるため、ダウンタイムに伴う損失が軽減されます。さらに、設備の稼働効率が可視化されることで、無駄なエネルギー消費や不要な人員配置を見直すことができ、電気代や人件費の削減も期待できるでしょう。
また、品質が安定することで不良品や再加工の発生を抑制でき、材料費の無駄を削減できます。データに基づいた発注や在庫管理が実現すれば、過剰在庫の削減にもつながるなど、さまざまな面での経営効率の向上に貢献するでしょう。
人材不足の解消
製造業では、熟練技術者の引退と若年層の人材不足が深刻な課題となっています。IoT技術の導入により、これまで熟練工が行っていた感覚的な判断や経験則に頼る作業をデータに基づく管理に置き換え、業務の属人化を防ぐことが可能です。
また、現場の情報が可視化されることで、遠隔地からの監視や少人数によるオペレーションも現実的になり、省人化や効率化が進みます。さらに、作業手順や工程がデジタル化されることで、新人や非熟練者でも一定レベルの作業が行えるようになり、教育コストの削減や人材の早期戦力化にもつながるでしょう。
異常や故障の予防保全
IoT化により、設備の稼働状態を常時監視し、異常兆候を早期に発見する予防保全(Predictive Maintenance)が可能になります。
従来の定期点検では、問題が顕在化するまで対処できないことが多く、突発的な機械トラブルによるライン停止が大きな損失となっていました。IoTによってセンサーから振動や温度、圧力などのデータを収集・分析することで微細な変化を察知し、事前に対策を講じることができます。
これにより、保守作業のタイミングを最適化し、無駄な部品交換や修理コストも削減可能です。安全性の向上にも貢献し、作業員の安心・安全な労働環境づくりにもつながるでしょう。
製造業におけるIoT化の課題
製造業におけるIoT化の課題としては、主に以下の3つが挙げられます。
コストが発生する
IoT化を進めるうえで、初期導入コストは大きな課題です。センサーや通信機器の設置や既存設備との連携、ネットワークインフラの整備、さらにデータを管理・分析するためのシステムやクラウド環境の構築には、相応の費用がかかります。導入後も保守やアップデート、データ保存などの運用費用が継続的に発生します。
まずは、小規模な範囲から段階的にIoTを導入し、データを活用した改善効果を可視化・数値化することで費用対効果を評価しながら進めましょう。一度に工場全体に導入するのではなく、中長期的な導入計画を検討することも大切です。
専門の人材が必要になる
IoTシステムを導入・活用していくためには、ITやデータ分析に関する知識を持った専門人材の存在が不可欠です。しかし、製造業ではIoT関連のソフトウェアやネットワーク、AI、セキュリティといった分野に対応できる人材が不足しているケースもあるでしょう。
また、現場の技術者とIT部門の間に認識のギャップがある場合、導入や運用がスムーズに進まないこともあります。社内での人材育成に取り組むと同時に、外部の専門企業のサポートを受けるのも方法のひとつです。
システムの継続的な管理が必要になる
IoTは導入するだけでなく、適切な運用が大切です。たとえば、センサー・デバイスの定期的な点検や故障対応や通信状況の確認、収集されたデータの整理・保管、分析システムのアップデートなど、多くの管理作業が継続的に必要になります。
加えて、インターネットを介して機器がつながる以上、サイバー攻撃やデータ漏洩といったセキュリティリスクにも常に備える必要があります。これらの維持・運用には、現場側と情報システム部門の密な連携が欠かせません。
製造業でIoT化を進めるステップ
製造業の現場でIoT化を進めるには、以下の3つのステップが重要です。
可視化
IoT化の最初のステップは可視化です。製造現場の状況を正確に把握するため、機械設備にセンサーを取り付け、稼働状況・温度・振動・圧力・エネルギー使用量などの情報をリアルタイムで収集します。
これにより、人の感覚や経験に頼っていた作業が、数値データとして見えるようになり、誰でも現場の状態を把握できるようになります。可視化されたデータは、生産のボトルネックや設備の無駄な動作などを発見する手がかりにもなるでしょう。
設備の制御
データが可視化できたら、設備の制御に取り組みます。収集したデータを活用して生産設備の動作を自動で調整・管理するフェーズです。
たとえば、温度が一定の基準を超えた場合に自動的に冷却ファンを作動させる、特定の条件下で機械の動作を一時停止するなどが、可視化されたデータに基づく設備の制御にあたります。現場の状況に応じたリアルタイムな対応が可能です。
これにより、オペレーターによる手動操作や判断の手間が減り、安定稼働と品質のばらつきの低減が実現します。さらに、遠隔からの制御も行えるようになれば、多拠点の工場を少人数で管理することも可能になり、省人化や効率化も期待できるでしょう。
自動化
最後に、可視化されたデータに基づく設備の制御を自動化します。設備同士が相互に連携し、収集したデータをもとにAIなどを活用して生産工程を自律的に最適化することを目指しましょう。
たとえば、ラインの進行状況を判断して、前後の機械のスピードを自動で調整したり、材料不足や異常があれば即座に別の工程に切り替えたりといった、柔軟な対応がこれに該当します。
これにより、常時人が介在しなくても安定した品質と高い生産性を維持できるスマートファクトリーが実現します。生産全体の効率が飛躍的に向上するほか、人的ミスの削減やコスト最適化にもつながり、競争力の強化にも大きく貢献するでしょう。
製造業におけるIoT活用例
製造業におけるIoTの活用例を3つ紹介します。
活用例①:自動車部品工場における生産ラインの可視化と改善
ある自動車部品の製造工場では、既存設備にセンサーを後付けし、製造ラインの稼働状況や作業サイクルをリアルタイムで記録・可視化するIoTシステムを導入しました。各工程の生産数や稼働率をクラウド上で一元管理することで、現場の改善活動が容易になり、実際に複数のラインで生産効率が30%以上向上しました。
また、データをスマートフォンなどからも確認できるようにすることで、現場の管理者が時間や場所にとらわれず状況を把握できるようになりました。
活用例②:金属加工業における工作機械の稼働監視と品質向上
金属加工工場では、工作機械にセンサーと通信機器を取り付け、加工中の主軸負荷や電流値をリアルタイムで収集するシステムを構築しました。
これにより、加工条件の最適化が進み、不良率の低下や加工時間の短縮といった成果が得られています。また、設備の稼働状況をスマートデバイスで監視できる仕組みによって、少人数体制でも複数の機械を効率よく管理できるようになり、省人化にもつながりました。
活用例③:多拠点工場の統合管理
国内外に複数の生産拠点を持つ製造企業では、各工場の設備データをIoTで収集し、共通のプラットフォーム上で一括管理できる体制を整えています。
これにより、各拠点の稼働率やトラブル情報を本社側で即時に把握でき、生産計画の変更やトラブル対応を迅速に行えるようになりました。オープンソース技術を活用することで社内外の関係者とデータを共有しやすくし、継続的な改善活動も活性化されています。
まとめ
本記事では、製造業におけるIoT化のメリットや活用例などを解説しました。IoT化には導入コストがかかるものの、生産性や品質の向上だけでなく、長期的にはコスト削減にもつながります。多くの企業がIoTを現場に導入し、業務効率の改善などを達成しています。
IoT化は、データの可視化・設備の制御・自動化の3つのステップで導入を進めることが可能です。はじめは小規模に導入をスタートし、費用対効果などを評価しながら導入範囲を広げていくとよいでしょう。
製品紹介
製造現場のIoT化には、自社の製品や製造に使う部品などの情報も可視化し、どこからでも閲覧できるようにしておく必要があります。こうしたさまざまなデータの可視化と共有には、PIM(商品情報管理)システムが応用できます。IoT化に活用するPIMシステムなら、商品情報管理システム「KOKONIDAS(ココニダス)」がおすすめです。
KOKONIDASでは、自社の製品はもちろん、その部品や原料に関する情報などもまとめて一元管理できます。情報はリアルタイムに更新され、権限のある社内関係者がチェック可能です。
<KOKONIDASの特徴>
- リーズナブルなコストで気軽に導入できる
- システムの知識は不要で、誰でも簡単に操作できる
- パッケージ化されているため、早期運用開始ができる
KOKONIDASの詳しい機能や特徴はこちら
KOKONIDASはデモ環境での無料体験もご利用いただけます。現場のIoT化に向けたPIMシステムの導入を検討中の担当者様は、ぜひお気軽にお問い合せください。
KOKONIDASに関するお問い合わせはこちら